在三河口矿业公司百米井下,一场“变废为宝”的技术工艺正悄然改变着该矿的传统生产逻辑。他们以-320运输大巷矸石充填工程为“试验田”,创新应用分阶段复合充填工艺,将矸石变废为宝、吃干榨净,探索出一条“技术降本、循环增效、绿色生产”的可持续发展路径。
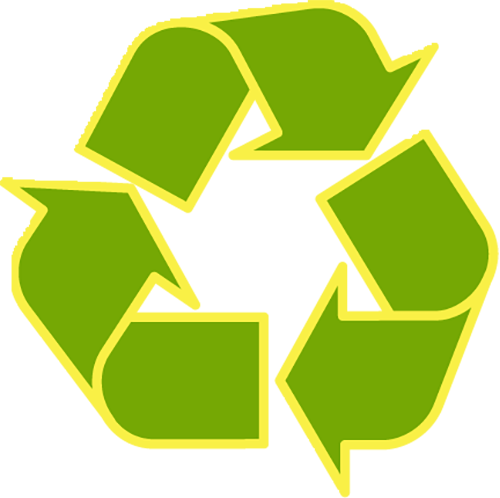
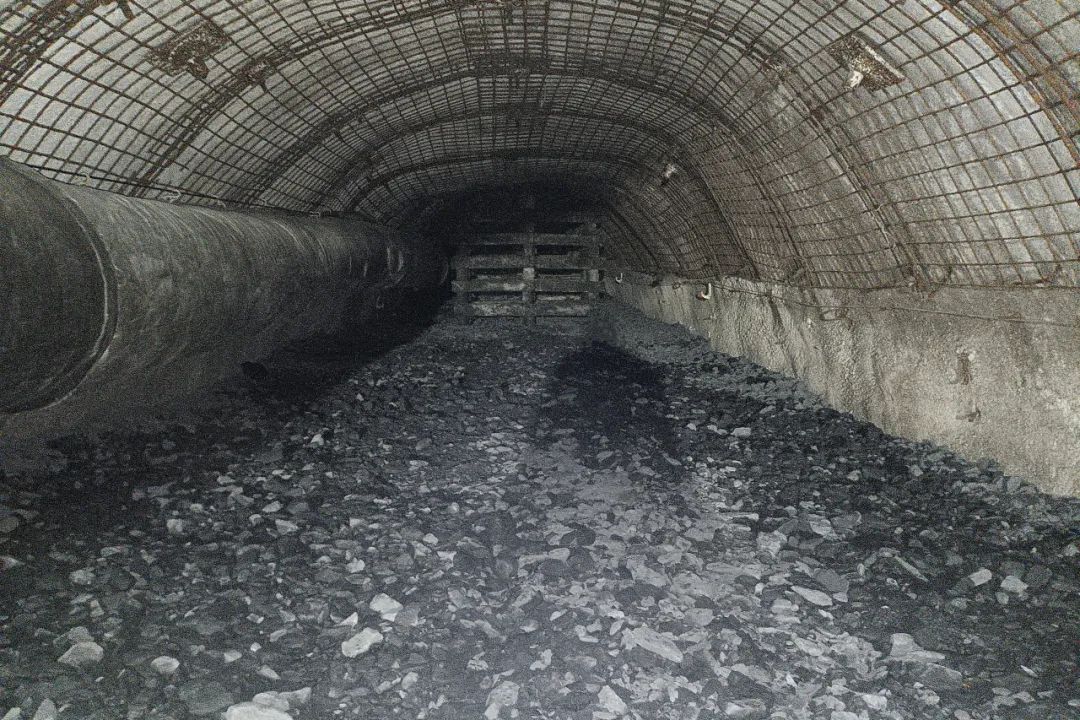
传统上,煤矿选煤生产产生的洗矸存放处置,既占用土地又存在环保风险,为了让矸石从“生态包袱”变成“绿色财富”,他们结合实际,提出“分阶段复合充填”方案,针对巷道层间距小于3米的区段,采用“无机快凝充填密闭材料+洗矸”复合充填工艺,对3至6米过渡区段,则用“洗矸+废旧水泥轨枕”工艺。
他们组织施工人员对立交层间距小于3米的区段进行充填,完善现场的压风、供水、供风、供电系统,安装双液气动注浆泵、搅拌罐和注浆管路,并在充填位置的末端砌筑一道全断面挡墙。在双液气动注浆泵的轰鸣声中,A、B料液在搅拌罐内快速融合,地面洗矸装车后运输到井下进行充填,用时13天就完成了70m³的巷道充填。

在施工层间距3至6米的区段,满载洗矸的电机车穿梭如织,废旧水泥轨枕在这里“重获新生”。他们先以洗矸填充至2米高度,剩余空间再以废旧水泥轨枕搭建“井”字形支撑垛,用时26天就完成了600m³巷道充填。
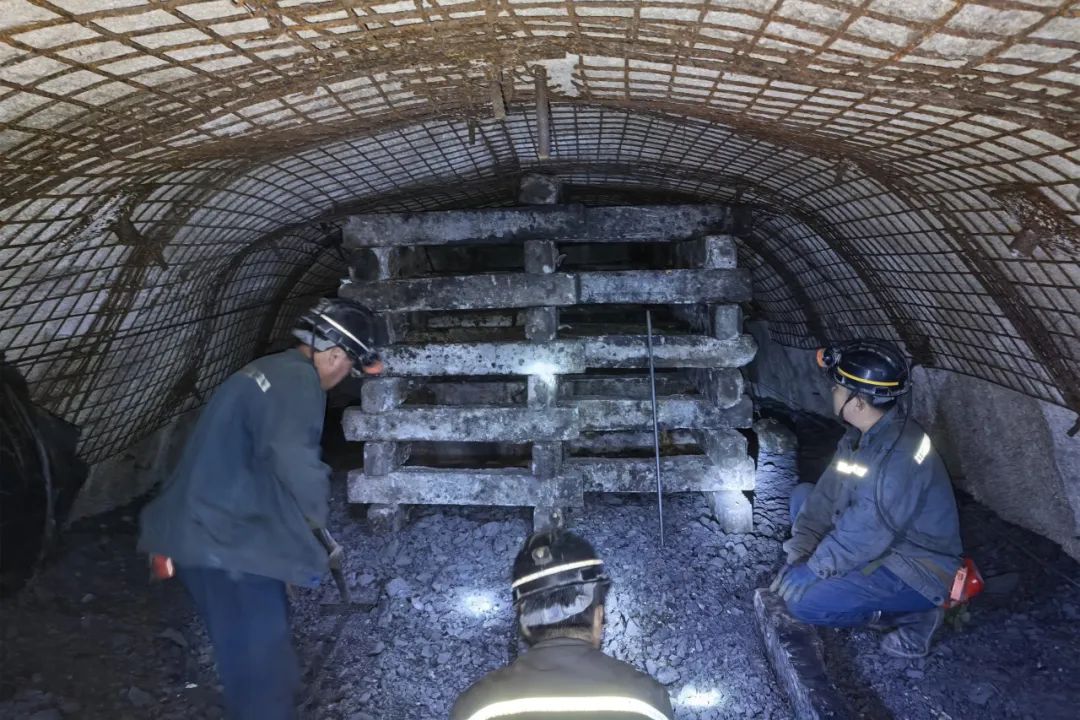
“施工中,我们还将一部分井下TDS系统筛选后的矸石作为充填材料,既减少地面尾矿堆积,又节省新材料成本,减少副井提升电费。”该公司掘进副总师田军说。
据了解,该公司井下充填工程原计划需要施工39天、耗资83.9万元,但是在全体施工人员的共同努力下,他们最终以26天、40.6万元成本高效收官,在这组数字背后,是一套“技术+管理”的双轮驱动体系。
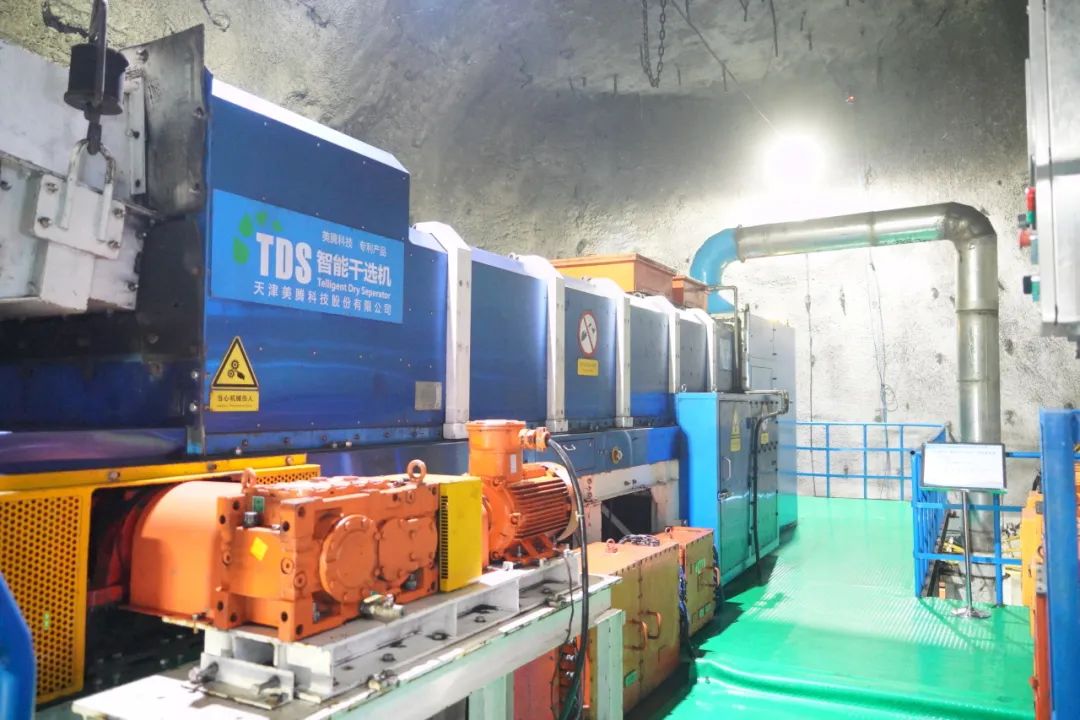
他们采取“模块化”施工模式,将120米充填段拆解成多个单元,每个单元实施“勘察—备料—充填—验收”四步闭环管理,地面装矸、井下运输、现场施工三线并行,工序衔接精确至小时级。充填期间,他们建立跨部门协同机制,每天召开工程施工总结会议,对存在问题及施工工艺进行优化论证,破解了设备调度、材料运输等难题。同时,实施“项目制”考核,在充填区域施工期间进行划片分包,明确每班运输车次、矸石方量、轨枕支设数,完成率与绩效工资挂钩。
“降本增效不是‘抠门’,而是智慧;绿色低碳不是‘负担’,而是机遇。下一步,我们将持续探索充填新技术新工艺,努力实现矸石井下‘消化’,推动矿井绿色发展。”三河口矿业公司经理车本方说。